This clamp is an integral part of the Aluminum Formwork System, a highly efficient and standardized construction solution designed specifically for cast-in-place concrete structures. It provides coordinated control over key processes such as steel reinforcement, concrete pouring, and embedded mechanical/electrical installations.
Back Waler Clamp
The Back Waler Clamp, used in conjunction with square steel pipes, ensures that wall formwork remains straight, level, and flat during concrete pouring—particularly at the base of the wall. It effectively prevents deformation and guarantees superior wall quality.
Key Features
Aluminum Formwork System Overview
The Aluminum Formwork System is an efficient and standardized construction method designed for forming cast-in-place concrete structures, while also coordinating the scheduling of rebar installation, concrete pouring, and mechanical and electrical conduit placement.
System Advantages
- Fast Construction: Simultaneously forms walls, floor slabs, columns, beams, stairs, window hoods, balconies, and decorative features, greatly improving construction efficiency.
- High Dimensional Accuracy: Ensures precision in concrete structures for consistent and precise door and window fitting.
- Excellent Surface Finish: Produces smooth, off-form concrete surfaces, eliminating the need for additional plastering work.
- Simple and Flexible Operation: Easy to assemble and disassemble, lightweight, and adaptable to various architectural designs.
- Cost-Effective: Components have a long service life and can be reused hundreds of times, reducing the average cost per use significantly.
Technical Specifications
Iterm One
Iterm two
Iterm There
Iterm Four
Case Study
We believe the projects that we have executed speak for themselves. CITIC HIC has engineered and provided 6 AG mills of Ø12.2m×11m (28000kW gearless drive) and 6 overflow discharge ball mills of Ø7.9×13.6m (2×9000kW gear drive) for Sino Iron Project in Australia. For Zijin Mining’s Duobaoshan Copper Mine project in Heilongjiang, we have manufactured and provided SAG mills of Ø11×6.4m (2×9000kW) and overflow discharge ball mills of Ø7.9×13.6m (2×9000kW) which have been well operating currently.
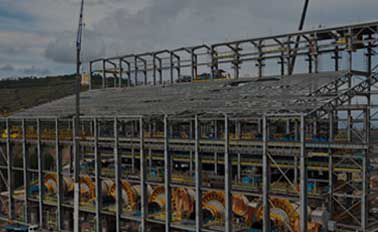
Brazilian Miner Vale SA
23 large-scale ball mills, Ø5.5×8.8m
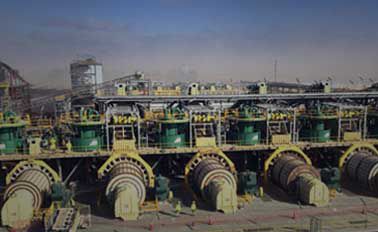
Wengfu Phosphate Mine Project Phase II in Saudi Arabia (Ma'aden)
6 wet grinding rod mills, Ø4.6×6.7m
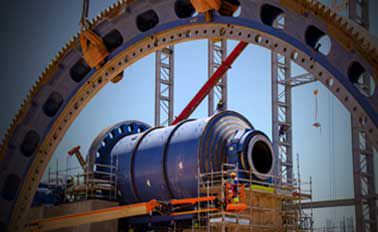
Vedanta Project in South Africa
1 SAG mill, Ø8.5×5.5m
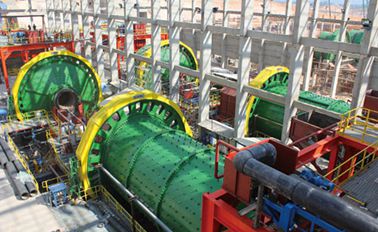
Laos Phonesack Group's KSO Gold Mine Project (83,000t/d)
6 SAG mills, Ø8.8×4.8m

Mongolian Erdenet Mining Corporation's Copper Mine Project (20,000t/d)
SAG mill, Ø9.75×4.88m
Full-process Solution for Mineral Grinding
We believe the projects that we have executed speak for themselves. CITIC HIC has engineered and provided 6 AG mills of Ø12.2m×11m (28000kW gearless drive) and 6 overflow discharge ball mills of Ø7.9×13.6m (2×9000kW gear drive) for Sino Iron Project in Australia. For Zijin Mining’s Duobaoshan Copper Mine project in Heilongjiang, we have manufactured and provided SAG mills of Ø11×6.4m (2×9000kW) and overflow discharge ball mills of Ø7.9×13.6m (2×9000kW) which have been well operating currently.
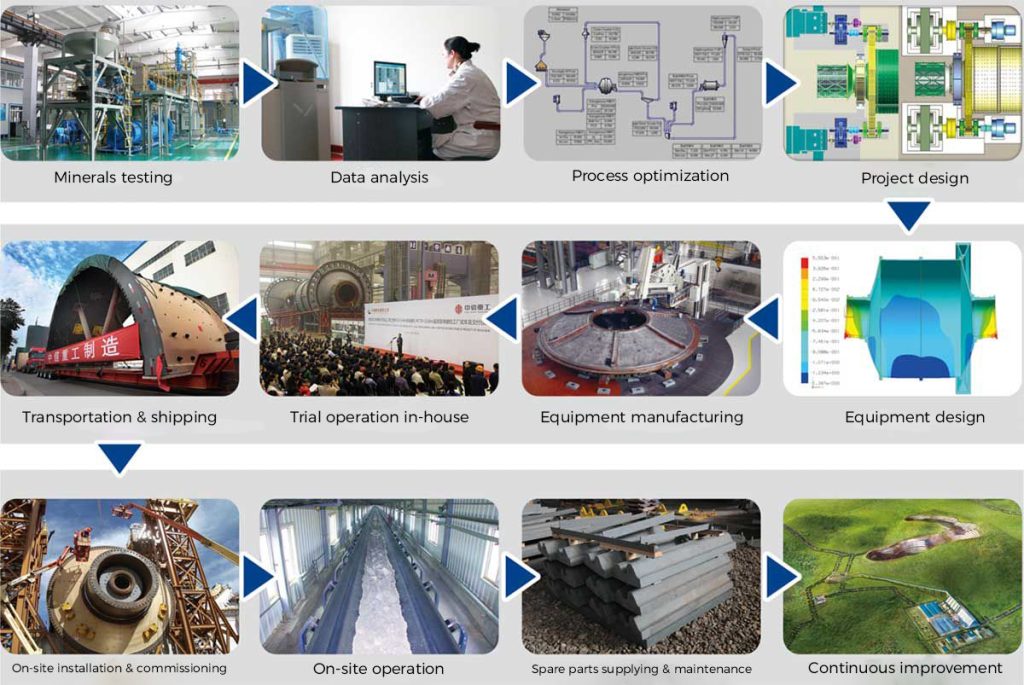
Why Choose CITIC HIC's Grinding Mills
- High cost-effectiveness
CITIC HIC grinding mills are recognized as China’s Manufacturing Industry Single Champion Product. CITIC HIC is responsible for setting the national standards of semi-autogenous mills (SAG mills) and ball mils, supported by powerful database, optimized process technology, cutting-edge design concept, and 60 years of experience in developing and nurturing innovative technology. - High operating rate
The long life cycle of our products is based on the adoption of international standards, high-quality materials, state-of-the-art processing techniques. - Low-carbon & environmental-friendly processes
Intelligent control technology coupled with long-life wear-resistant materials results in low-carbon and eco-friendly operations. - High-efficiency service
Our service network is distributed all over the world, and our service team of seasoned professionals is reliable and willing to assist along the way. We are able to deliver quick response to customer needs and provide full life cycle support via online monitoring and diagnosing, product upgrading and continuous process improvement.