Precision-engineered, the aluminum alloy beam system is widely used in structural construction, delivering reliable support and outstanding stability. It excels in demanding environments due to its lightweight, corrosion resistance, and ease of installation, making it an ideal choice for high-rise buildings, bridges, formwork systems, and other structural applications.
Aluminum Alloy Beam System
Our Aluminum Alloy Beam combined with matching keels significantly reduces labor and material costs on construction projects. Compared to traditional timber beams, our aluminum beam system offers:
-
Up to 1/3 fewer horizontal components
-
Up to 1/2 fewer vertical supports
-
Dramatically reduced weight per unit, lowering worker fatigue and increasing construction efficiency
-
Greater advantages with increased supporting heights
Key Features
Key Features & Advantages
✅ 1. Enhanced Safety by Design
Wider flange design improves beam stability and resists tipping, reducing the risk of accidents and worker injuries. Fewer incidents lead to shorter downtimes and lower insurance costs.
✅ 2. Stronger Materials
Crafted from high-strength 6351-T6 structural aluminum alloy, our beam is tougher than common 6061-T6 materials. Reinforced side flanges resist deformation, hold beam clamps firmly, and reduce the need for repairs—translating into more time spent on productive work.
✅ 3. Faster Installation
Angled T-slot design allows quick alignment and connection, accelerating setup and improving flexibility in managing tight schedules or unexpected changes on-site.
✅ 4. Flexible & Cost-Effective
Modular and adaptable—can be used with wooden or plastic inserts to fix plywood formwork. The hollow section allows insertion of 2×4 or 2×6 wooden studs to extend beam length as needed, reducing inventory. Reusable and durable, easy to store and transport, contributing to overall project cost savings.
✅ 5. Higher Construction Efficiency
Features 12mm (½ inch) T-slot channels, simplifying the connection between beams and cross braces. This improves work efficiency, reduces labor costs, and directly boosts project profitability.
Technical Specifications
Iterm One
Iterm two
Iterm There
Iterm Four
Case Study
We believe the projects that we have executed speak for themselves. CITIC HIC has engineered and provided 6 AG mills of Ø12.2m×11m (28000kW gearless drive) and 6 overflow discharge ball mills of Ø7.9×13.6m (2×9000kW gear drive) for Sino Iron Project in Australia. For Zijin Mining’s Duobaoshan Copper Mine project in Heilongjiang, we have manufactured and provided SAG mills of Ø11×6.4m (2×9000kW) and overflow discharge ball mills of Ø7.9×13.6m (2×9000kW) which have been well operating currently.
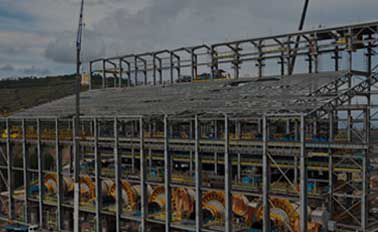
Brazilian Miner Vale SA
23 large-scale ball mills, Ø5.5×8.8m
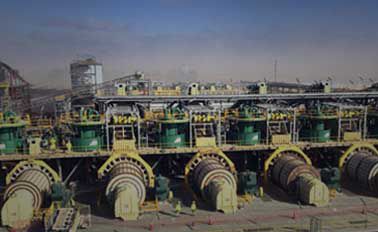
Wengfu Phosphate Mine Project Phase II in Saudi Arabia (Ma'aden)
6 wet grinding rod mills, Ø4.6×6.7m
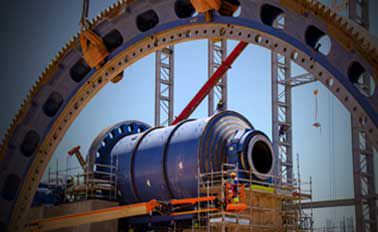
Vedanta Project in South Africa
1 SAG mill, Ø8.5×5.5m
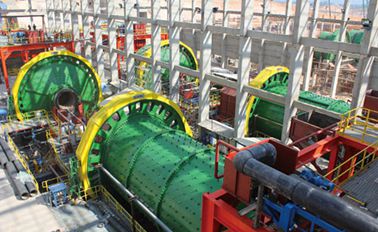
Laos Phonesack Group's KSO Gold Mine Project (83,000t/d)
6 SAG mills, Ø8.8×4.8m

Mongolian Erdenet Mining Corporation's Copper Mine Project (20,000t/d)
SAG mill, Ø9.75×4.88m
Full-process Solution for Mineral Grinding
We believe the projects that we have executed speak for themselves. CITIC HIC has engineered and provided 6 AG mills of Ø12.2m×11m (28000kW gearless drive) and 6 overflow discharge ball mills of Ø7.9×13.6m (2×9000kW gear drive) for Sino Iron Project in Australia. For Zijin Mining’s Duobaoshan Copper Mine project in Heilongjiang, we have manufactured and provided SAG mills of Ø11×6.4m (2×9000kW) and overflow discharge ball mills of Ø7.9×13.6m (2×9000kW) which have been well operating currently.
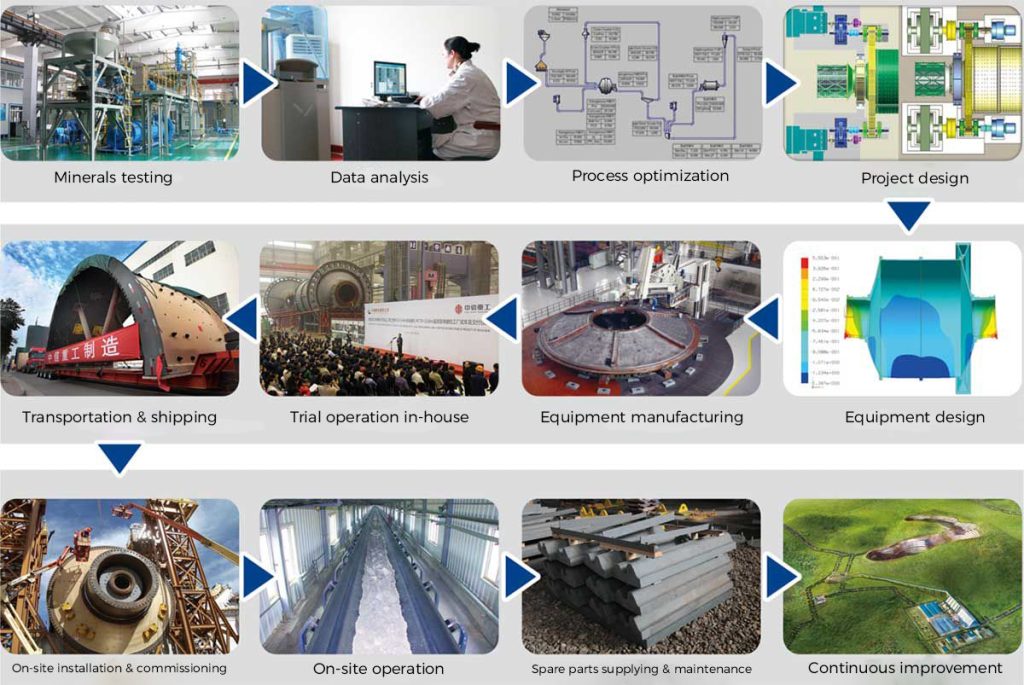
Why Choose CITIC HIC's Grinding Mills
- High cost-effectiveness
CITIC HIC grinding mills are recognized as China’s Manufacturing Industry Single Champion Product. CITIC HIC is responsible for setting the national standards of semi-autogenous mills (SAG mills) and ball mils, supported by powerful database, optimized process technology, cutting-edge design concept, and 60 years of experience in developing and nurturing innovative technology. - High operating rate
The long life cycle of our products is based on the adoption of international standards, high-quality materials, state-of-the-art processing techniques. - Low-carbon & environmental-friendly processes
Intelligent control technology coupled with long-life wear-resistant materials results in low-carbon and eco-friendly operations. - High-efficiency service
Our service network is distributed all over the world, and our service team of seasoned professionals is reliable and willing to assist along the way. We are able to deliver quick response to customer needs and provide full life cycle support via online monitoring and diagnosing, product upgrading and continuous process improvement.